We have TRIED to make a perfect sweat in larger quantities for years... And it's finally happening!!! Two new styles, the Zero Waste Sweatshirt and the Short Sleeve Turtleneck, are almost complete! They'll ship in time for Christmas ;)
The Process.
The process of designing and developing a new style is more complicated, expensive, and time-consuming than you may think! Here's how we did it.
1. Fabric Selection and Testing
We sourced a new bamboo/cotton blend terry fabric and matching rib, prioritizing softness and washability as always! We ran a shrink test before committing to this fabric. This entails washing and drying a test panel, and then measuring the percentage of vertical and horizontal shrinkage to make sure that the final garments will shrink proportionally when prewashed. Choosing colors was the most difficult part, since there were so many great options. We ended up going with a dusty rose and a mossy green.
Fabric Cost: $15/yard (Averaging $21.30 for each Zero Waste Sweat and $14.62 for each Short Sleeve Turtleneck)
2. Design

I always design our new styles based on what I think our customers will love and wear often. This makes our pieces pretty timeless! For our two terry styles, I settled on a Zero Waste Sweatshirt and a Short Sleeve Turtleneck. I sketched out each one, and Mackenzie and I discussed details such as stitching, length and general fit.
Design Cost: 2 hours at $30/hour for my time (not counting the hours laying awake at night thinking about these!). A total of $60 for design.
3. Sampling
We always sample out new styles to see if we're happy with the general idea and fit. We start with a rough pattern and then cut the fabric pieces. Nowadays, we'll sample each piece in both XS and 2XL (so both Mackenzie and I can try one on!). The first sample of the Sweatshirt came out almost perfect! The only thing we needed to change was to make the sleeve cuff a little tighter. The Turtleneck looked nice in the XS, but in the 2X it felt too short, with the sleeve way too loose. We corrected the patterns based on this and then sent cut pieces to our producton partners, Opportunity Threads, to make the second and final samples.
Sampling Cost: Fabric cost was $123.90. I spent 3 hours cutting and sewing samples, costing us $90. We paid Opportunity Threads $56.48 for the second samples. Total, $270.38.
4. Grading
Once we received second fit samples from Opportunity Threads and were happy with the results, I was ready to grade the patterns. This means making final pattern pieces in all sizes, XS-4XL. Because we used the same pattern for the Zero Waste Sweat as we did for our original t-shirt, I only had to grade the sleeves for this style. For the Short Sleeve Sweatshirt, I had to fully grade the front, back, and sleeves. Each pattern piece must fit with the other pieces just like a puzzle! Altogether, I graded a total of 32 pattern pieces for these styles.
Grading Cost: Pattern paper cost was about $20. I spent 6 hours grading, costing us $180. Total, $200.
5. Production
The next and final step was production. We decided to cut these styles in-house because we wanted to be very specific with the amounts per size and per color. This was exhausting for me and took a lot of mental work to keep everything straight. It was a relief to package all of the cut pieces off and send them to Opportunity Threads, where they will be sewn. After we get the sweatshirts and turtlenecks back, we'll need to sew in size tags and prewash them all!
Production Cost: I spent 20 hours cutting, which I valued at a total of $400. Opportunity Threads charges us $7.50 per piece to sew sweatshirts and $6.75 per piece to sew turtlenecks. We'll pay $200 total for shipping back and forth, and about $240 to tag and wash all of the garments. Total production: $1702.50
*Figuring Out Price
Pricing our items is always a bit of an art. But we begin with our flat production costs (in the case of the Zero Waste Sweatshirt, for example, the cost is about $39 per piece). We must factor in all of the additional costs that go into running a business, including marketing and advertising, rent, photoshoot, and tools/machines. For the Sweatshirt, we settled on a final price of $128. In all honesty, it's a bit low for how expensive the fabric was... But the inherent value of a sweatshirt is usually lower than that of a woven piece. In addition, the costs of design, sampling, and grading are only needed one time. If we do another run of sweatshirts, we won't have those extra costs!
More stories
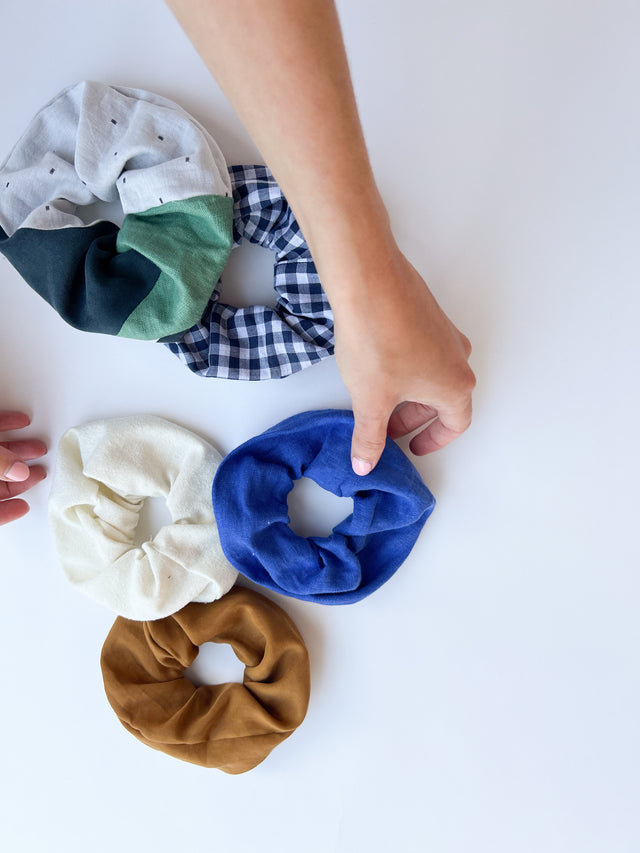
Scrunchie DIY
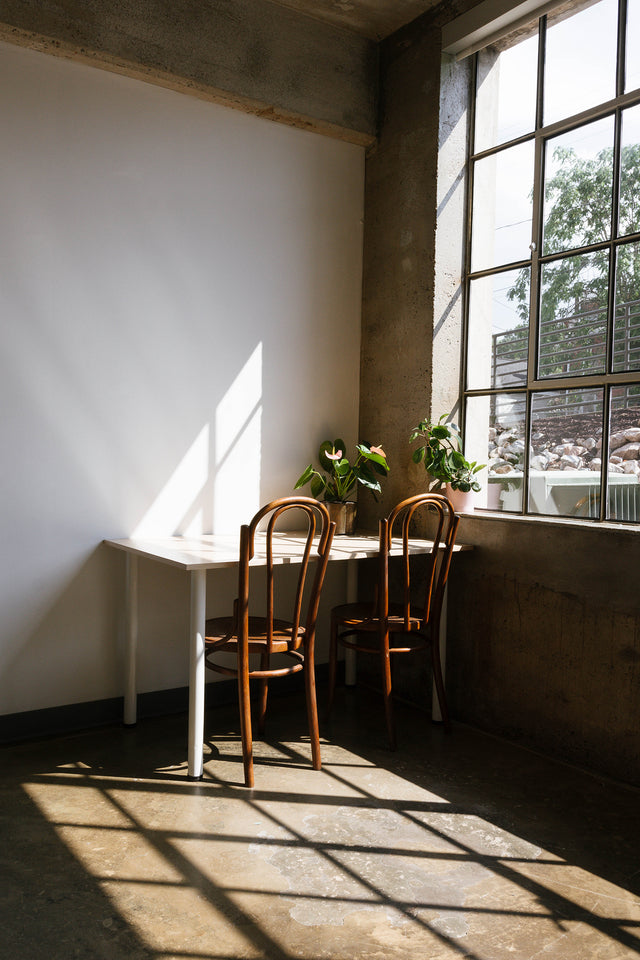